Advances in Robotic Manipulators and Their Applications
A special issue of Applied Sciences (ISSN 2076-3417). This special issue belongs to the section "Robotics and Automation".
Deadline for manuscript submissions: closed (31 January 2024) | Viewed by 11572
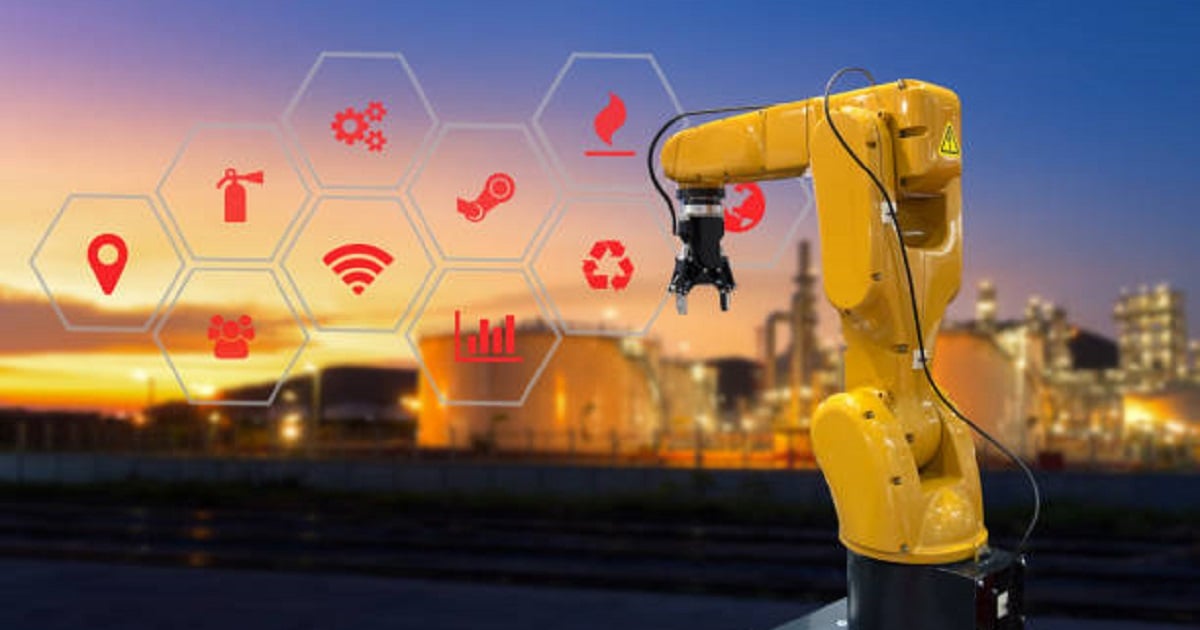
Special Issue Editors
Interests: computer vision; expert systems; robotics; motion analysis
Special Issues, Collections and Topics in MDPI journals
Interests: mobile robotics; AI in robotics; data fusion; human-machine interaction
Special Issues, Collections and Topics in MDPI journals
Special Issue Information
Dear Colleagues,
The interaction of robotic manipulators with their environment has always been an active topic in robotics. Robotic grasping is one of the fundamental and most challenging skills of robots. It demands robotic perception of the environment, planning, and control.
The research focus for grasping and manipulation has evolved from rigid manipulators and specialized grippers to robotic arms and hands that can perform various tasks in unstructured environment and scenarios.
This Special Issue will be dedicated to new advances and findings in hardware and software solutions for robotic manipulators.
Subjects that will be discussed in this Special Issue will focus on robotic hand design, hand sensor and actuator design, force and tactile sensing, grasping force control, user interfaces, multimodal sensing, sensor-based control, grasping planning and contact modelling, as well as artificial neural networks in intelligent grasping and manipulation. We welcome papers presenting multidisciplinary and state-of-the-art research and applications of robotic manipulators in various fields, such as agriculture, industry, and human-robot interaction.
Prof. Dr. Vladan Papić
Dr. Josip Musić
Guest Editors
Manuscript Submission Information
Manuscripts should be submitted online at www.mdpi.com by registering and logging in to this website. Once you are registered, click here to go to the submission form. Manuscripts can be submitted until the deadline. All submissions that pass pre-check are peer-reviewed. Accepted papers will be published continuously in the journal (as soon as accepted) and will be listed together on the special issue website. Research articles, review articles as well as short communications are invited. For planned papers, a title and short abstract (about 100 words) can be sent to the Editorial Office for announcement on this website.
Submitted manuscripts should not have been published previously, nor be under consideration for publication elsewhere (except conference proceedings papers). All manuscripts are thoroughly refereed through a single-blind peer-review process. A guide for authors and other relevant information for submission of manuscripts is available on the Instructions for Authors page. Applied Sciences is an international peer-reviewed open access semimonthly journal published by MDPI.
Please visit the Instructions for Authors page before submitting a manuscript. The Article Processing Charge (APC) for publication in this open access journal is 2400 CHF (Swiss Francs). Submitted papers should be well formatted and use good English. Authors may use MDPI's English editing service prior to publication or during author revisions.
Keywords
- grasping control
- robotic hands
- robotic hardware control
- robotic manipulators
- robotic perception